Na „PIT FoodCon 2023: Tradicija i inovacije, okusi budućnost(i)!“, konferenciji posvećenoj prehrambenoj industriji Bosne i Hercegovine, među izlagačima važno je mjesto imala konsultantska kuća Targer Engineering & Consulting koja je predstavnicima prehrambene industrije predstavila Lean metodologiju te učesnike zainteresirala za njezinu samostalnu implementaciju.
Uime kuće Targer govorila je Mirela Begić – Pecar, Lean inžinjerka. “Lean metodologija u prehrambenoj industriji Bosne i Hercegovine neznatno je prisutna. Nažalost, o njoj se čak i ne zna mnogo. Benefiti koje donosi primjena ove metodologije su, međutim, nevjerovatni”, naglasila je tom prilikom Begić–Pecar.
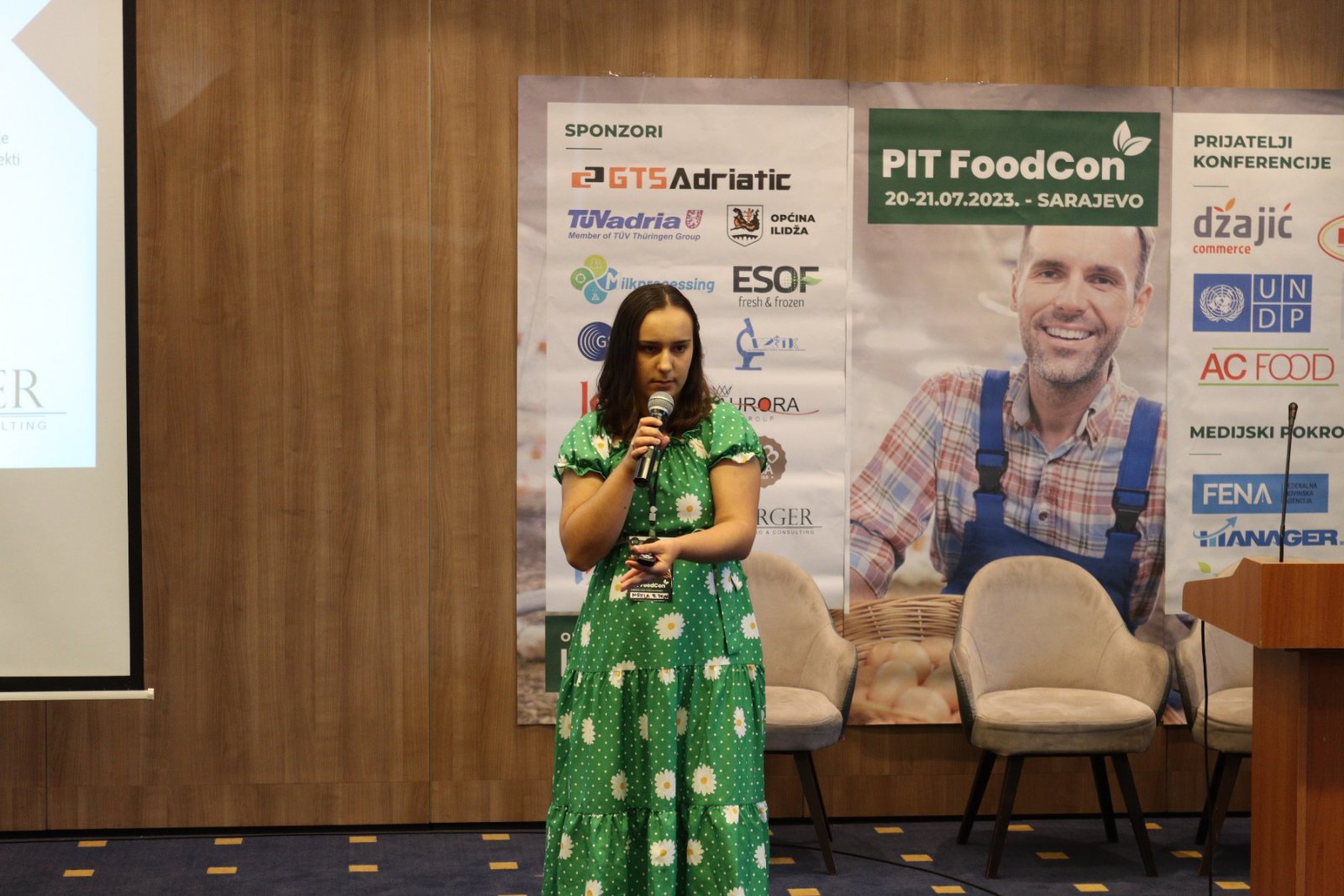
Šta je Lean, koje metode podrazumijeva i kakvim se sve alatima možete koristiti prilikom njegove implementacije mnogo smo govorili i pisali. Stoga, ovom prilikom navodim samo osnovnu činjenicu da se Lean ne može kupiti niti instalirati, jer, naprosto, to je filozofija i metod olakšavanja rada i eliminaciju gubitaka koji vodi ka izvrsnoj produktivnosti i organizaciji rada a dolazi iz Toyote, gdje se izvorno naziva Toyota proizvodni system.
Predstavnike prehrambene industrije pozivamo da se odvaže i implementiraju Lean. Podsjećamo da ovo putovanje nije nimalo lagano, ali je itekako vrijedno truda, riječi su Begić-Pecar.
Stanje na tržištu iz dana u dan sve je kompliciranije te su za uspjeh i značajnija postignuća nužna nova znanja i vještine. U tome smislu, “istraživati Lean, učiti o svim njegovim mogućnostima te uopće pojmiti ga kao nešto neophodno svakoj industriji koja želi opstati, rasti i premašiti konkurenciju može biti od suštinske važnosti.”
Prema rezultatima istraživanja, samo 11 posto kompanija u prehrambenoj industriji ima uvedenu organizaciju radnih mjesta po 5S modelu. To je poražavajuća činjenica! I govori u prilog prijedloga da promjena organizacije proizvodnje u prehrambenoj industriji treba početi odatle.
Prvo to! Sortitaj. Složi. Sredi. Standardiziraj. Sprovedi.
Organizacija radnih mjesta po 5S metodu donijet će dugoročne rezultate, doprinijet će poboljšanju produktivnosti proizvodnje, olakšanju rada i zadovoljstvu uposlenika. Ma koliko se u početku opirali svakoj promjeni, u konačnici svi bivaju zadovoljniji.
Nakon toga, slijedi Kaizen. “Previše je opasno provesti radni dan u kojem niste konzumirali barem gram Kaizena. Kaizen ima zaista značajnu nutritivnu vrijednost za vašu proizvodnju”, riječi su Begić-Pecar. Mala, kontinuirana i održiva poboljšanja. Okupite tim i bavite se Kaizenom. Najlakše je kroz Quick Kaizen program. Quick Kaizen program je implementacije malih poboljšanja s težnjom ka stalnim poboljšanjima unutar proizvodnih pogona kompanije uz minimalne, odnosno, nikakve novčane investicije. Fokus programa je na malim, ali održivim poboljšanjima do kojih se dolazi u kratkom period. Shodno temi, bira se tim ljudi koji će se baviti problematikom. Najčešće su to timovi od četiri do osam osoba. Kao odlična metodologija za ovaj program pokazala se Toyotin A3 metod za rješavanje problema, jednostavan za komunikaciju svim učesnicima.
Iz Targera je predstavljen i jedan primjer ovakvog projekta iz prakse. Riječ je o projektu Poboljšanja rada na mašinama jednog odjela koji ima pet mašina, koje opslužuju tri radnika. Projekt je pokrenut s ciljem smanjenja troškova odjela, a na prijedlog tim lidera ovog odjela za cilj je postavljeno i da se uvedu neradne subote za ovaj odjel, a prethodno su se radile 2 subote u mjesecu. Koristeći se A3 metodologijom, definirano je trenutno stanje, prikupljeni i analizirani podaci i definiran plan akcija koje su vodile do optimizacije procesa, odnosno ostvarenja zadatih ciljeva. Nakon što su postignuti očekivani rezultati, ova metodologija usvojena je na nivou kompanije, te se projekti ove vrste redovno otvaraju u svakom od odjela. Ciljevi su različiti, kao i potrebe, ali put do ostvarenja je manje više isti i uvijek zahtijeva implementaciju sitnih akcija koje se baziraju na upotrebi Lean alata.
Sada se ovi projekti vode prema dnevniku u kojem su isplanirani vremenski okviri, teme i timovi i iz kojeg se vidi u kojoj fazi je koji projekt. Kompletna kompanija usvojila je ovu metodu rješavanja problema. Ovim pristupom, i proizvodni radnici su dosta uključeni u teme shodno svojim poslovima i time je postignut dodatni efekt. Svega nekoliko kratkih i usmjerenih radionica, nekoliko bezazlenih akcija od kojih se nećete pošteno ni umoriti, zagarantirano će dati rezultate.
Siguran uspjeh svakoj proizvodnji donosi i eliminacija gubitaka. Iako se, nažalost, vrlo često okrećemo tradicionalnim načinima povećanja produktivnosti (ubrzaj mašinu, ubrzaj čovjeka, uštedi na kvalitetu…), to ipak nije dugoročno rješenje. Jer, i mašina i čovjek radit će ubrzanim tempom samo neko vrijeme, a onda? Onda, problem! Zato, umjesto toga, fokusirajte se na eliminaciju gubitaka. Odnosno, bavite se olakšanjem rada. Posmatraje svoje procese i uočite gdje sve gubite. Gdje gubite vrijeme, energiju i, naravno, novac. Lean metodologija prepoznaje 7 vrsta gubitaka (transport, zalihe, nepotrebne pokrete, čekanje, prekomjernu obradu, prekomjernu proizvodnju i greške) te se bavi njihovom eliminacijom ili minimalizacijom (u ovisnosti od toga mogu li se potpuno eliminirati ili ih možemo samo minimizirati, npr. ne možemo eliminirati transport u procesu, ali možemo pronaći najkraće moguće puteve).
Veoma je važno posmatrati kako se zaista odvijaju vaši procesi i to zabilježiti. Ne to kako bi trebali da se odvijaju, niti to kako mislite da se odvijaju, nego kako se zaista odvijaju. Provedite vrijeme direktno u procesu. Opažajte i bilježite sve što se dešava. Što više realnih podataka, to bolje. Zatim vizualizirajte te podatke (grafikoni, simogrami, spaghetti dijagrami…)! Da ne kažemo, nacrtajte i obojite.
Zatim analizirajte uzroke problema. Postoje različite metode za to: Ishikawa dijagram, Pareto analiza, 5 zašto, 6-3-5 metoda… Iskoristite bilo koji metod, ali pronađite glavne uzroke. I na kraju, definirajte i provedite akcije kojima ćete ukloniti uzroke problema. Nema sumnje, da će vas logika voditi na definiranje akcija koje će podrazumijevati implementaciju različitih Lean metoda. Neće biti lahko, ali će vrijediti, sigurno!
Još jednom, prehrambena industrijo, odvaži se i kreni u implementaciju Lean-a. Jer, vrijeme je da naši proizvodi u svijetu prehrambene industrije postanu ono što je Toyota u svijetu automobilske industrije.
Krajnje vrijeme!