Transportna kolica od drveta koja mogu pomjerati dijelove karoserije nisu samo održiva, već teže samo 145 kilograma, umjesto uobičajenih 400 kilograma kod kombinovane konstrukcije od čelika, aluminija i plastike. To donosi uštedu u težini od 64 posto.
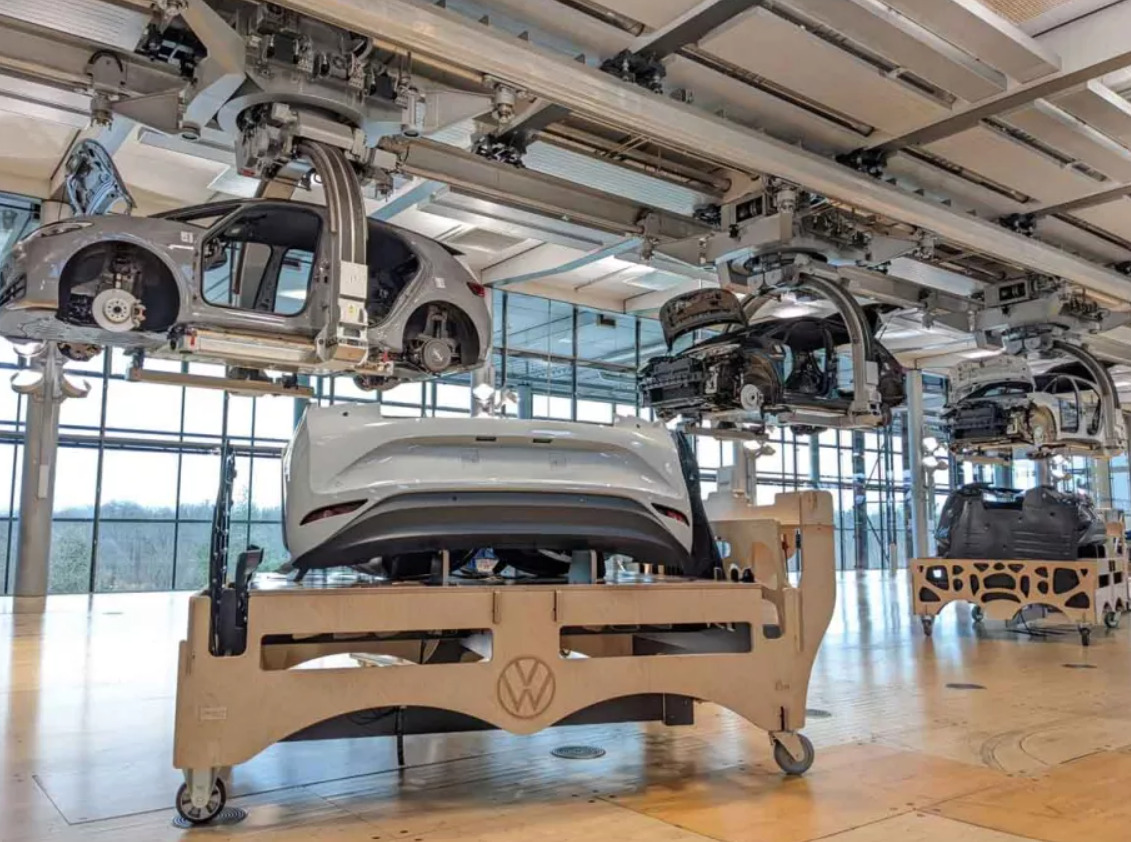
Startup Ligenium je uspio da drvo prvenstveno etablira kao nosač tereta u intralogistici i automobilskoj konstrukciji, kao i u mašinstvu – i već je profitabilna kompanija u Njemačkoj. “Produktion” je razgovarao s generalnim direktorom Christophom Altom o istoriji nastanka, uspjesima i neverovatnim činjenicama ovog startupa.
Christoph Alt objašnjava da on i njegove kolege dolaze iz istraživačkog okruženja sa skoro 15 godina iskustva. Na Univerzitetu u Chemnitzu, fokus je bio na tehnologiji primjene obnovljivih materijala na odsjeku za mašinstvo. Zadatak je bio otkriti kako se obnovljive sirovine mogu ponovo učiniti društveno prihvatljivim u kontekstu inženjeringa postrojenja i tehnologije transporta.
Drvene komponente otporne na kemikalije
“U suštini, ovo je proizašlo iz teme hemijske otpornosti, odnosno rudarstva, transportnih sistema i izgradnje rudnika soli. Čak je i nehrđajući čelik tamo korodirao. Zato smo počeli da razmatramo drvo kao materijal. „Ne samo da smo otkrili hemijsku otpornost, već i pogodnost za laganu konstrukciju“, kaže Alt.
Tim je zatim kreirao proračunske modele, principe dimenzioniranja, metode konstrukcije i opće metode gradnje od drveta u mašinstvu. Tema su bili i proizvodni procesi i tehnologija povezivanja.
“U 2015. godini imali smo prvi serijski pilot u pogonu u fabrici u Wolfsburgu u sklopu Chemnitz University of Technology. Postojala je prva drvena pokretna traka dugačka 250 metara – koja je i danas u Wolfsburgu,” zadovoljno kaže generalni direktor.
Prednosti na prvi pogled
Christoph Alt sažima prednosti drvenih nosača tereta:
„Neposredne troškovne prednosti rješenja drvenog nosača tereta leže prvenstveno u stepenu punjenja. Što više komponenti stane u isti volumen, potrebno je manje nosača tereta. Ovo smanjuje ukupni transportni napor u logističkom lancu.
Osim toga, nosači tereta također osiguravaju viši kvalitet komponenti. To znači da se komponente ne izgrebu tako brzo kada se koriste za rukovanje nosačem tereta prilikom umetanja i istovara.
Ako je nosač tereta oštećen, pojedini dijelovi se mogu zamijeniti na licu mjesta jer je to neka vrsta Lego sistema. To znači da nisu potrebni složeni procesi zavarivanja i ispravljanja.
Međutim, specijalni nosači tereta koji se pomiču viljuškarom, naprimjer, ne mogu biti u potpunosti izrađeni od drveta. Također koristimo modularne metalne elemente koje pričvršćujemo na lokalni udar viljuške viljuškara ili kao zaštitu rubova.
Veće tržište i veća korist, također u smislu održivosti, leži u procesu ulazne logistike.
U skladu s tim, kvalitet komponenti, razina punjenja u kombinaciji s mnogo različitih optimizacija logističkih procesa i lagana konstrukcija predstavljaju problem. Tu je i ergonomski aspekt. Nosače tereta također guraju ljudi, s tim da su klasični nosači tereta ponekad teški 300 kilograma sa komponentama. Naši nosači tereta imaju samo 150 kilograma.”
Zabrinutost zbog požarnog opterećenja i vlage je neosnovana
Ali upravo zato što je, prema Alt-u, funkcionisao tako dobro, naučnici su se suočili s velikim izazovom. „Zato što kada krenete u proizvodnju s ovim materijalom, javlja se zabrinutost zbog požarnog opterećenja i vlage . Često se kaže da drvo gori i bubri“, objašnjava Alt.
Ali to su pitanja koja se mogu držati pod kontrolom. „Samo ga morate dobro pripremiti, a zatim u skladu sa tim razjasniti sa specijalističkim odjelima“, naglašava Alt. Do 1950-ih godina u mašinstvu je bilo čak i istraživanja drveta. Međutim, ovu temu brzo su zamijenili čelik, aluminij i plastika.
Ali Alt pokazuje promjenu igre, kako su drvo učinili društveno prihvatljivim u mašinstvu uprkos svim otporima: „Mi smo svoje znanje protumačili s trenutnim stanjem umjetnosti iz drugih područja – naprimjer lakih kompozitnih vlakana – u naša područja obnovljivih sirovina. Iz ovoga smo stvorili nove temelje. “To nas je toliko uvjerilo da smo osnovali Ligenium,” kaže Alt.
Drvo se ne može definisati brojkama
“Mi dolazimo iz mašinstva i stoga smo obučeni na odgovarajući način. Drvo više ne igra ulogu u ovom obrazovnom sektoru. Ako se godinama bavite plastikom, metalima i drugim klasičnim materijalima, imate poseban pristup materijalima. Međutim, drvo zahtijeva potpuno drugačiji pristup, jer je drvo živi materijal”, naglašava Alt.
Zato drvo nije moguće definirati brojkama. “Barem ne unutar tako uskog okvira kao što je to obično slučaj s materijalima koji su standardizirani, već s drvetom imamo relativno veliku raznolikost”, opisuje Alt. Pogotovo se materijal mijenja u klimatskom kontekstu u odnosu na vlažnost zraka. “Ako to ne uzmete u obzir, možete imati problema s materijalom”, upozorava Alt.
Drvo se ističe u održivosti i laganoj konstrukciji
Također, teme vlažnosti i općenite vlažnosti, ovisno o tome je li drvo izloženo direktno vodi, moraju se vrlo pažljivo uzeti u obzir. “Proveli smo mnogo istraživanja o tome. Međutim, ta istraživanja uvijek su idealizirana. Na kraju, to treba dokazati u praksi, a praksa često donosi nepravilne scenarije korištenja”, kaže Alt. Ti su scenariji teško predvidljivi.
Ako se, prema Altu, ne uzmu u obzir takvi nepravilni scenariji unaprijed, jer ih se matematički ne može obuhvatiti, skloni smo ponovno pasti u stare obrasce, posebno u područjima gdje smo već vješti – poput čelika ili aluminija, dodaje Alt.
Prije nekoliko godina, naglašava, aspekt održivosti nije bio toliko prisutan kao danas. “To, međutim, nije bila naša osnovna namjera, jer je uvijek bila tehničke prirode. Zanimljivo je da je tehnički portfelj drva u mnogim aspektima uvijek bio održiv. Također i u laganoj konstrukciji”, ističe Alt.
Drveni materijali kao jeftinija alternativa aluminiju i čeliku
“Lagana konstrukcija često je vrlo skupa. Samo pogledajte oblasti od karbonskih vlakana ili komplicirane aluminijske strukture te laganu konstrukciju od čelika. To sve nije jeftino. Međutim, s drvetom je to jednostavno izvedivo”, izvještava Alt.
Ligenium također ne koristi samo čisto prirodno drvo. “Naši drveni materijali su modifikovani s najvećim mogućim naglaskom na održivost, tako da vlažnost i temperatura imaju manji utjecaj u našim konstruktivnim primjenama. Osim ako ne počne gorjeti, tada imamo problem, ali vlažnost držimo pod kontrolom”, uvjeren je Alt.
Drvo ostaje oblikovno stabilno – čak i stabilnije nego što bi to bilo prirodno. “To je zato što koristimo furnirano drvo. Furniri su zalijepljeni pod pravim uglom jedan na drugi, što ih čini stabilnijima”, pojašnjava Alt.
Poznavanje drvene konstrukcije nadoknađuje nedostatak standardizacije
“S obzirom na to, materijali koje koristimo su prilično dobro standardizirani. Nadalje, s našim znanjem, možemo ući u tehnološke primjene koje su više opterećene od onoga što proizvođač navodi, a što ne bi učinio neko ko se ne razumije u materijal”, naglašava Alt.
“Jer, imamo dugo iskustvo od otprilike 15 godina u ovom području. Iskreno rečeno, to je gotovo neuhvatljivo, jer je to iskustvo neophodno. Jer drvo se ne može jednostavno staviti u formulu. Ali radimo na tome”, dodaje Alt s osmijehom.
Područja primjene u tehnologiji transporta i kao robotska ćelija
“Dakle, mogu se obuhvatiti primjene od tehnologije transporta do modernih robotskih ćelija koje predstavljaju nosive strukture u kontekstu mašinogradnje. To su oba trajno pouzdane strukture koje se mogu koristiti u industriji prema našem shvatanju”, ističe Alt.
Tehnologija transporta razvijena je u saradnji s partnerom koji razvija tehnologiju transporta i distribuira aerodromsku tehnologiju. “Međutim, ne smatramo se samo proizvođačem logističkih nosača tereta, već kao korisnici novog materijala – kao osnovna tehnologija gdje se danas koriste čelik, aluminij ili plastika.
Primjena u automobilskoj industriji: Značajno smanjena težina
Put Ligeniuma u automobilsku industriju konačno je imao i malo sreće. “Dvaput sam imao sreću dok sam bio na raznim logističkim događajima na kojima su bili prisutni i proizvođači automobila. Tada sam uspostavio kontakt s jednim njemačkim proizvođačem automobila – i našao vrlo velikog ljubitelja drva”, prisjeća se Alt.
Proizvođač automobila imao je teška čelična kolica – s 140 kilograma pocinčane čelične strukture. “Proizvođač automobila bio je zainteresiran za pilot-projekt s nama u okviru svoje tadašnje strategije Green Logistics. Projekt je bio vrlo uspješan, jer smo smanjili težinu nosača za pola”, kaže Alt.
Po transportnom vozilu moglo se uštedjeti i do pola tone CO2 – isključivo bilančno samo zamjenom materijala. Naime, na jednu tonu pocinčanog čelika otpada otprilike tri tone CO2 emisija.
Značajna ušteda težine kod transportnih vozila
“U slučaju transportnog vozila u staklenoj manufakturi u Dresdenu, ušteda težine bila je još značajnija. Transportno vozilo od 400 kilograma izrađeno od čelika, aluminija i plastike mogli smo zamijeniti vozilom od 145 kilograma od drva”, izračunava Alt. Prema Altu, kroz klasično transportno vozilo u okoliš dospije otprilike dvije tone CO2, dok je bilanca CO2 drvenog nosača čak klimatski pozitivna. “U transportnom vozilu od drva veći je udio vezanog CO2 nego što je nastalo tijekom proizvodnje materijala”, ističe Alt.
Zanimljivo je da nosač tereta od drva također ima sposobnost ESD (elektrostatičko pražnjenje), što vozilo u čeličnoj izvedbi nema. Zbog toga se mora modificirati s provodljivom plastikom. “Drvo se može koristiti kao provodljiva struktura s odgovarajućim premazom. Može biti izolirajuće, gdje nema provodljivosti, ali ni antistatika. Ili može biti provodljivi nosač tereta. To je vrlo zanimljivo za elektromobilnost, jer su svugdje integrirani kontrolni dijelovi, čak i u braniku”, objašnjava Alt.
Skaliranje nosača tereta od drveta
Prema Christophu Altu, skaliranje je lako provodivo. Ipak, opisuje prepreke u trenutačnoj proizvodnji.
“Uvijek to uspoređujem s LEGO kockama, gdje imam određeni standardni set dijelova. Svaki novi set uvijek uključuje još dva do tri posebna dijela. Ovi posebni dijelovi moraju se razviti jer, na primjer, odražavaju konturu dijela ili imaju novu funkciju. Ili imaju novu vezu s periferijom transportne tehnike. To zahtijeva vrijeme za razvoj i naša je najveća prepreka.
S druge strane, pripremu rada možete – ako je konstrukcijski sklop dobar – automatizirati jednim pritiskom na gumb. To nije prepreka.
Proizvodnju na stroju također je potpuno moguće automatizirati. To je poznato iz industrije namještaja, gdje se također radi na velikoj skali. Bitno je gdje se stroj nalazi, jer je potrošnja energije za obradu drveta upravljiva.”
Postoji i prepreka pri montaži. No, u osnovi, ta prepreka postoji i kod čeličnih nosača tereta, jer se tamo još uvijek vrše zavarivanje, lakiranje i pocinčavanje. To je puno veći napor nego izrada i sklapanje LEGO sistema”, objašnjava.
Alt ističe da Ligenium koristi drvene materijale s potpunim porijeklom. “Od proizvodnje materijala do faze korištenja i recikliranja. Sve mora ponovno ući u ciklus. Jer s obnovljivim resursima možemo raditi cirkularno i na kraju uvijek izvaditi energiju ili, primjerice, proizvesti bio-ugljen (biljni ugljen).
“Kada se uzme u obzir da sedam posto svjetskih emisija nastaje tokom proizvodnje metala, bilo bi vrlo korisno smanjiti jedan posto toga drvom u strojarstvu”, razmišlja Alt naglas. Prema tome, jedan posto globalnih emisija zamijenjen je obnovljivim resursima pod tehnički zahtjevnim uvjetima. “Mi sami to nećemo postići, ali potencijal svakako postoji”, ističe Alt.
Digitalizacija nosača tereta
Međutim, direktor ide korak dalje jer želi digitalizirati nosače tereta. “Imamo viziju cirkularne ekonomije i imamo viziju digitalizacije cirkularne ekonomije odnosno obnovljivih resursa i prikazivanja klimatski neutralne cirkularne ekonomije, bilo da je to fizički ili digitalno”, objašnjava Alt.
Jer, radi se o laganim, održivim i ekološkim nosačima tereta. U njih će se ugraditi senzorika kako bi se na kraju digitalizirao lanac opskrbe. “Ako se nosači tereta od drveta koriste u logistici, to možda čini pet do deset posto životnog ciklusa. No, znatno veći dio dolazi iz faze korištenja”, ističe Alt. Jer, u automobilskoj industriji, nosač tereta se pomakne deset puta dnevno, ponekad i preko 30 kilometara – i to tokom sedam godina u sustavu od tri smjene. To je kontinuirano.
“Nosilac tereta ponekad je samo pola sata na traci i onda se vraća. Ovdje se primjenjuje koncept lagane izgradnje, koji naravno ima utjecaj na troškove prijevoza”, zaključuje Alt. To se može isto tako integrirati i u digitalni blizanac, kao i tema punjenja, tako da se mogu smanjiti logistički troškovi.
Digitalni blizanac drvenog nosioca tereta
“Sve to mogu uključiti u digitalni blizanac nosioca tereta i tako znam njegovu poziciju i koje putove prelazi. Na taj način mogu razvijati čitavu logistiku s obzirom na održivost, što opet dovodi do prednosti u procesima”, kaže Alt.
U vezi s tim, Ligenium zajedno s SAP-om i drugim partnerima gradi održivu financijsku imovinu. “Time želimo digitalno pripremiti sve održive pokazatelje koji se pojavljuju tijekom fizičkog životnog ciklusa. Stoga su pod uvjetima EU taksonomije sposobni za izvještavanje, moguće je pratiti lance opskrbe i pružiti pokazatelje o pakiranju”, opisuje Alt.
Prema tome, ova učinkovitost može se prikazati s obzirom na troškove refinanciranja. “Onda ne mislite samo da je drvo održivo, već to mogu i dokazati. Ako su niži troškovi dokazivi, tada će se i češće kupovati, a održivost će se jače promicati. Jer iz EU taksonomije proizlazi da se održivo ponašanje financijski nagrađuje”, zaključuje Alt.
. . .
Tekst Leichter und nachhaltiger: Holz als Trumpf im Maschinenbau autora preveden je s portala Produktion.