Na konferenciji Targer LeanCon, održanoj 22. i 23. juna 2023. u Banjoj Luci bilo je govora o primjeni Lean metodologije iz ugla inžinjera. Uime konsultantske kuće Targer Engineering & Consulting govorila je Lean inžinjerka Mirela Begić-Pecar ponudivši učesnicima praktične fore i fazone industrijskog asfalta s ciljem lakše samostalne primjene ove metodologije.
“Osnovna djelatnost kuće Targer jeste uvođenje Lean metodologije u proizvodne kompanije širom Bosne i Hercegovine”, istakla je tad Begić-Pecar.
Ako ste propustili ovu konferenciju, u nastavku pročitajte koje to fore i fazone možete i sami primijeniti u svojoj proizvodnji.
Lean metodologija, bazira se na eliminaciji gubitaka, odnosno olakšanju rada, koji dovode do poboljšanja produktivnosti i ostvarivanja ciljeva kakvi su poštivanje rokova isporuke, nivo kvaliteta, optimizacija zaliha, što u konačnici znači optimizaciju lead time-a, odnosno protočnog vremena.
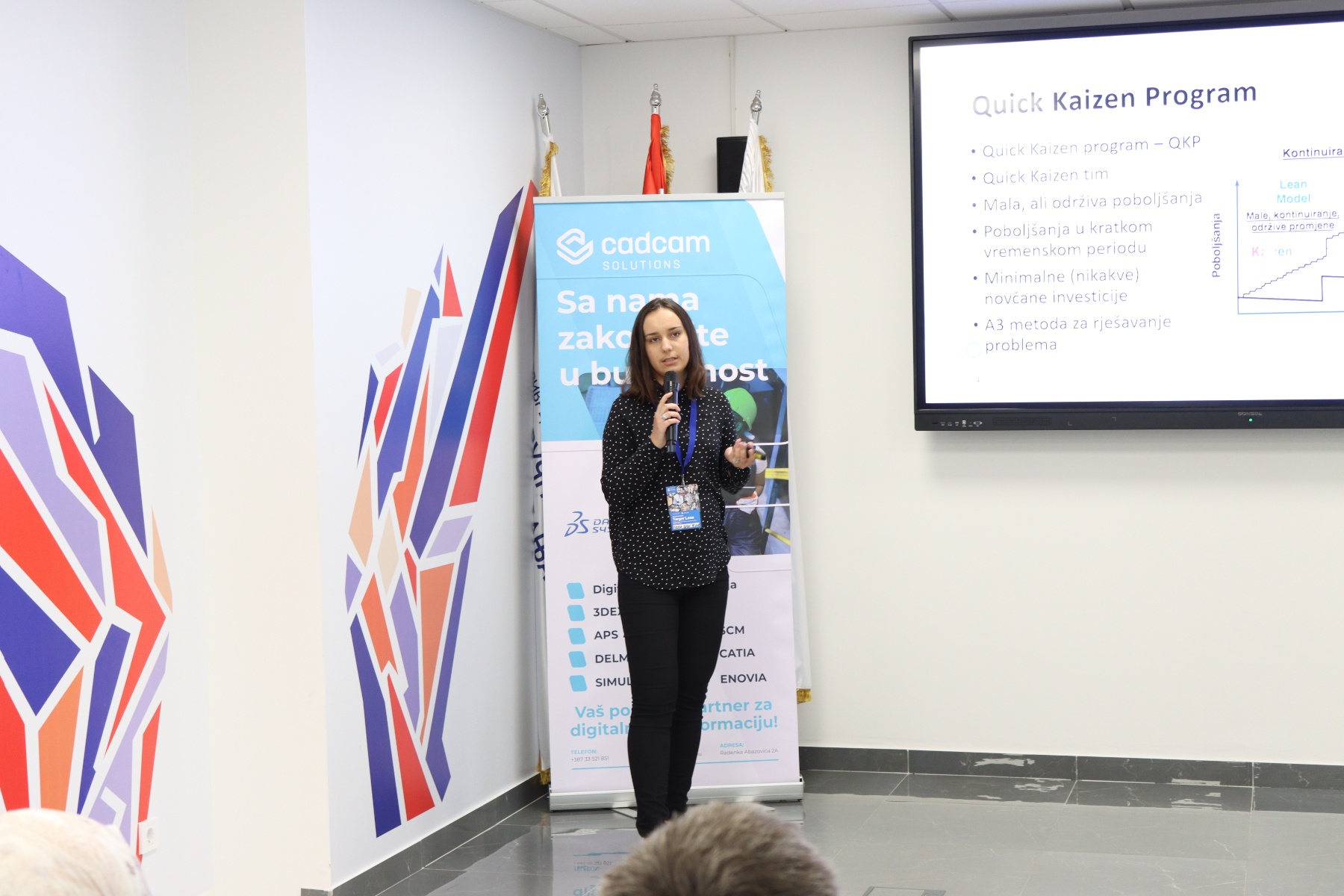
Ako već niste, predlažemo da istražite pojmove kao što su: Kaizen, 5S, 7 vrsta gubitaka, OEE, SMED, Poka-Yoke, Vizual menadžment. Jednostavno istražujući ove pojmove, dobit ćete ideje koje će vas voditi ka poboljšanju. Zatim ćete otkrivati nove pojmove koje treba istražiti, nove ideje. Proces poboljšanja nikad se ne završava a Lean nikada ne stavlja tačku.
Svaka proizvodnja treba se zasnivati na 5S metodologiji za organizaciju radnog mjesta. Ovo je važna tema oko koje, međutim, nema rasprave: naprosto, ovo je obaveza koju je svaka proizvodnja trebala izvršiti – jučer! Vrlo jednostavno, u pet koraka, organizujte radna mjesta koja će vam omogućiti protočnost proizvodnje i poboljšanje produktivnosti.
Sortiraj. Složi. Sredi. Standardiziraj. Sprovodi.
Jedna od Targerovih fora predstavljenih na konferenciji jeste i tzv. Quick Kaizen program. Quick Kaizen program projekt je implementacije malih poboljšanja s težnjom ka stalnim poboljšanjima unutar proizvodnih pogona kompanije uz minimalne (nikakve) novčane investicije. Ovaj program fokus stavlja na mala, ali održiva poboljšanja do kojih se dolazi u kratkom vremenskom periodu. Shodno temi, bira se tim ljudi koji će se baviti problematikom. Najčešće su to timovi od četiri do osam osoba. Kao odlična metodologija za ovaj program pokazala se A3 metoda za rješavanje problema. Metoda dolazi iz Toyote i vrlo je jednostavna za komunikaciju svim učesnicima.
Iz Targera je predstavljen i jedan primjer ovakvog projekta iz prakse. Riječ je o projektu Poboljšanja rada na CNC mašinama u jednoj kompaniji čiji CNC odjel ima pet mašina, koje opslužuju tri radnika. Projekt je pokrenut s ciljem smanjenja troškova odjela, a na prijedlog tim lidera ovog odjela za cilj je postavljeno i da se uvedu neradne subote za ovaj odjel, a prethodno su se radile dvije subote u mjesecu. Koristeći se A3 metodologijom, definisano je trenutno stanje, prikupljeni i analizirani podaci i definiran plan akcija koje su vodile do optimizacije procesa, odnosno ostvarenja zadatih ciljeva. Nakon što su postignuti očekivani rezultati, ova metodologija usvojena je na nivou cijele kompanije, te se projekti ove vrste redovno otvaraju u svakom od odjela. Ciljevi su različiti, kao i potrebe, ali put do ostvarenja je manje više isti i uvijek zahtjeva implementaciju sitnih akcija koje se baziraju na upotrebi Lean alata.
Sada se ovi projekti vode prema dnevniku u kojem su isplanirani vremenski okviri, teme i timovi i iz kojeg se vidi u kojoj fazi je koji projekat. Kompletna kompanija usvojila je ovu metodu rješavanja problema. Ovim pristupom, i proizvodni radnici su dosta uključeni u teme shodno svojim poslovima i time je postignut dodatni efekt. Svega par kratkih i usmjerenih radionica, par bezazlenih akcija od kojih se nećete pošteno ni umoriti, zagarantovano će dati rezultate.
Dalje, ono što će sigurno donijeti uspjeh svakoj proizvodnji jeste eliminacija gubitaka. Iako se vrlo često (nažalost) okrećemo ka tradicionalnim načinima povećanja produktivnosti (ubrzaj mašinu, ubrzaj čovjeka, uštedi na kvalitetu…) to ipak nije dugoročno rješenje.
I mašina i čovjek radit će ubrzanim tempom samo određeno vrijeme, a onda? Problemi. Zato, umjesto toga fokusirajte se na eliminaciju gubitaka. Odnosno, bavite se olakšanjem rada. Posmatraje svoje procese i uočite gdje sve gubite. Gdje gubite vrijeme, energiju i naravno novac.
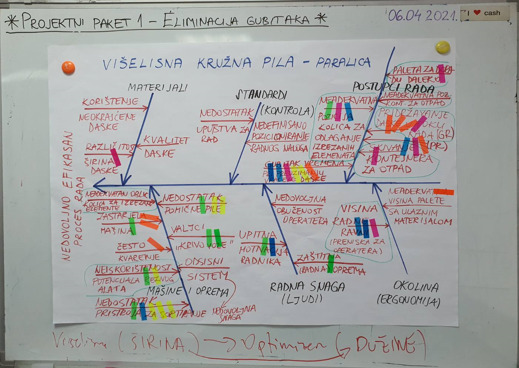
Lean metodologija prepoznaje sedam vrsta gubitaka (transport, zalihe, nepotrebne pokrete, čekanje, prekomjernu obradu, prekomjernu proizvodnju i greške) i bavi se njihovom eliminacijom ili minimalizacijom (u zavisnosti od toga da li se mogu potpuno eliminirati ili ih možemo samo minimizirati, npr. ne možemo eliminirati transport u procesu, ali možemo pronaći najkraće moguće puteve i sl.).
Veoma je važno posmatrati kako se zaista odvijaju vaši procesi i to zabilježiti. Ne to kako bi trebalo da se odvijaju, niti to kako mislite da se odvijaju, nego kako se zaista odvijaju. Provedite vrijeme direktno u procesu. Opažajte i bilježite sve što se dešava. Što više realnih podataka, to bolje.
Zatim vizualizirajte te podatke (grafikoni, simogrami, spaghetti dijagrami, …)! Da ne kažemo, nacrtajte i obojite. Zatim, analizirajte uzroke problema. Postoje različite metode za to: Ishikawa dijagram, Pareto analiza, 5 zašto, 6-3-5 metoda,… Iskoristite bilo koju metodu, ali pronađite glavne uzroke.
I na kraju, definirajte i provedite akcije kojima ćete ukloniti uzroke problema. Nema sumnje, da će vas logika voditi na definiranje akcija koje će podrazumijevati implementaciju različitih Lean metoda. Neće biti lahko, ali će vrijediti, sigurno!