Toyota proizvodni sistem (TPS) je arhetip Lean proizvodnje. Lean se često koristi kao sinonim za Toyotin proizvodni sistem, i to je generalno prilično tačno. Ponekad se naziva i „zapadnjačkom“ verzijom Toyotinog proizvodnog sistema. Međutim, postoje neke manje razlike u osnovnom pristupu, kao i neke veće i često nenamjerne razlike u njegovoj primjeni. Pogledajmo!
Razlika u terminologiji
Toyotin proizvodni sistem je filozofija i kultura Toyote o tome kako organizuju svoje procese, kako u proizvodnji tako i u drugim oblastima svog poslovanja. Koristi se u okviru Toyota grupacije, najpoznatije Toyota Motor Company, ali i mnogih drugih kompanija u njihovoj grupaciji, uključujući Denso, Toyota Industries, Aichi Steel, JTEKT, Toyota Auto Body, Aisin, Toyota Boshoku, Towa Real Estate, Toyota Motor East Japan, Toyoda Gosei, Hino Motors, Daihatsu, Toyota Housing Corporation i mog bivšeg poslodavca, Toyota Central R&D Labs.
Ova korporativna kultura i alati u njoj razvijali su se decenijama, počevši od osnivača Toyote, Sakichi Toyode. Po mom mišljenju, jedna od sjajnih stvari kod Toyote je njihova neumoljiva želja za poboljšanjem, gurajući prema istinskom sjeveru za mnoge generacije menadžera. Čak i danas, sistem se stalno razvija i mijenja. S druge strane, po mom mišljenju Denso je sada bolji u Toyotinom proizvodnom sistemu od samog Toyota Motor-a. Vjerujem da je vodstvo u Denso-u mnogo bolje od posljednjeg izvršnog direktora Toyota Motor-a, Akia Toyode.
Kompanije izvan Toyota grupacije često su koristile i prilagođavale ove pristupe. Problem je bio u tome što da ste u Daimler-u, ne biste mogli reći da koristite sistem konkurenta (Toyote).
Godine 1988, mladi student master studija, John Krafcik, koji je studirao kod Jamesa Womacka na MIT-u, napisao je rad o „Trijumfu sistema Lean proizvodnje“. Čuvena knjiga Womacka i dr. koja je popularizirala ovaj pristup, „Mašina koja je promijenila svijet“, pokupila je termin Lean proizvodnje. Ovo ime se zadržalo i od tada je Toyotin proizvodni sistem poznat kao Lean proizvodnja. Čak i sada, dvadeset pet godina kasnije, termin Lean je i dalje jak u industriji, uprkos brojnim pokušajima da se preimenuje u “Proizvodnja svjetske klase”, “Sinhrona proizvodnja”, “Operativna izvrsnost”, “Six Sigma” i još mnogo toga.
Razlika u sadržaju
Postoje neke razlike u sadržaju između Toyotinog proizvodnog sistema i Lean proizvodnje. Oni su rezultat kontinuiranog razvoja unutar i izvan Toyote. Dok kompanije izvan Toyote uvijek žele kopirati najnovije trendove unutar Toyote (a konsultanti su željni da im pomognu u tome), Toyota ne preuzima uvijek novi razvoj izvana.
Toyota svuda traži inspiraciju za poboljšanje svog proizvodnog sistema. U stvari, mnoge, MNOGE ideje za Toyotin proizvodni sistem potekle su izvan Toyote (npr. iz Ford-a, Junkers-a, Training within Industry programa, Nichib-a, Danly-ja i mnogih drugih). Toyota je prilično dobra u isprobavanju stvari, prikupljanju korisnih ideja i odbacivanju onih ne tako dobrih. Nisu svi razvoji izvan Toyote ušli u Toyotu. Evo (nepotpune) liste, zasnovane na mom znanju ili iskustvu. Neki od ovih dodataka mogu biti korisni, drugi ne toliko.
- Gubitak (Muda) zaista dolazi od Toyote, ali je mnogo izraženiji u zapadnom svijetu. Zapad je dodao i osmu vrstu gubitaka (neiskorištena ljudska kreativnost), ili čak više (pronašao sam do dvadeset četiri vrste gubitaka guglajući).
- Kaizen događaji za kratke sesije poboljšanja se ne koriste u Toyoti.
- Mapiranje toka vrijednosti (VSM) se u Toyoti zove analiza toka materijala i informacija (MIFA). Iako je to kamen temeljac u Leanu, to je samo manji i mnogo manje standardizovan alat u Toyoti.
- 5S kod Toyote je samo 4S. Zapadni dodatak od 5: Shitsuke za “Održi, samodisciplina” je za Toyotu isto što i 4: Seiketsu za “Standardiziraj”. Našao sam čak i izvore za 6, 7, pa čak i 8S (Shukan za “Stil”; i engleske riječi Safety and Security).
- Kata nije baš poznata u Toyoti, iako se poznata knjiga zove “Toyota Kata”.
- Hoshin Kanri je zaista iz Toyote, ali dobijam nedosljedne poruke o tome koliko se intenzivno koristi. Odvratni X-Matrix je, međutim, proizvod zapadnih konsultanata.
- Six Sigma takođe potiče iz Toyote. Pristup kvalitetu sa šest standardnih devijacija se zapravo ne koristi u Toyoti, iako se Six Sigma uspješno rebrandirala u Lean Six Sigma, dodavajući metode iz Toyotinog proizvodnog sistema.
- Metoda 8 D (Rješavanje problema osam disciplina) razvijena je u Fordu 1987.
- “14 principa upravljanja Toyotinog načina” Jeffreyja Likera pokušava sumirati filozofiju Toyote. Teško je sažeti filozofiju, ali ovo je jedan od popularnijih sažetaka.
- Za Pull proizvodnju, osim kanbana i tačke ponovnog naručivanja, postoje CONWIP, POLCA, Drum Buffer Rope i COPACABANA, ili (navodno također Pull) MRP vođen potražnjom (DDMRP).
- Cijeli koncept Industrije 4.0 za digitalizaciju cijele fabrike isproban je u Toyoti, ali je odbijen, iako, naravno, koriste i kompjutere i robote.
- Harada metoda za poboljšanje razvoja zaposlenih također dolazi iz Japana, ali ne iz Toyote.
Kontrola kvaliteta brze reakcije (QRQC) je Nissanov pristup upravljanju kvalitetom.
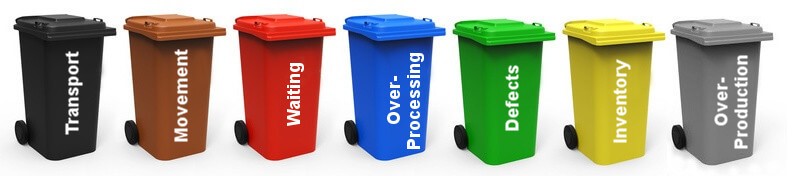
Ovo je samo kratka lista, a mogla bi biti mnogo duža. Ako želite više, pogledajte (trenutno) 469 unosa u mom Lean rječniku, od kojih su mnogi izvan Toyote.
Razlika u primjeni
Postoje i neke razlike u primjeni, ili, da kažem, u osnovnoj filozofiji. To je zbog različitih načina na koji se Lean radi u Toyoti i u zapadnom svijetu. Imajte na umu da ima PUNO generalizacije u sljedećim paragrafima, a da postoje kompanije izvan Toyote koje dobro izvršavaju Lean (npr. imam dobro mišljenje o Trumpf-u, ABB Stotz-Kontakt-u ili Kärcher-u, da spomenemo samo neke). Ima i dosta dobrih konsultanata (i ovdje prepuštam vama ako želite da me uvrstite na listu). Ali postoji mnogo više kompanija koje postižu manje od svog potencijala.
U Toyoti, Toyotin proizvodni sistem uglavnom rade ljudi Toyote, u velikoj mjeri oslanjajući se na ljude koji zapravo rade na procesima. U pogonu, to bi bili operateri na prvoj liniji. Oni dobro poznaju svoj sistem i veoma su zainteresovani da ga ne pogoršavaju „poboljšanjem“. Filozofija Toyotinog proizvodnog sistema prožima se kroz cijelu Toyotinu grupaciju.
Na Zapadu, sa Leanom često pomažu vanjski konsultanti. Oni obično ne poznaju sistem kao operateri, i moraju da impresioniraju osobu koja ih plaća… koja obično nije operater. Nažalost, impresionirati klijenta nije isto što i impresionirati operatere, a ponekad su operateri manje nego oduševljeni najnovijim promjenama. U nekim postrojenjima, “Lean” je čak i zabranjena riječ zbog prethodnih neuspjelih Lean projekata.
Također je teže generirasi promjenu kulture nego odraditi 5S radionicu, pa stoga Lean često više teži alatima i metodama nego osnovnim principima. Za to je ponekad krivo i vodstvo. Prečesto se na Lean gleda kao na neki alat koji se može kupiti i potom delegirati nekome u nižim rangovima hijerarhije. Ljudi ispod bi se trebali promijeniti, ali naravno ne i osoba na vrhu. Nažalost, dobar Lean počinje na vrhu, s mekim vještinama poput poštovanja prema ljudima. Takođe često otkrivam da, iako postoji mnogo toga za poboljšanje, kapacitet za poboljšanje je eliminisan kako bi se uštedio novac. Nadzornik koji je ostao u pogonu jednostavno nema vremena za poboljšanje.
Opet, ovo ne važi za sve zapadne kompanije i konsultante, a ima dosta onih koji su dobri i na pravom putu na svom Lean putovanju. Ali mnogo je onih gdje sistem ne ispunjava svoj potencijal. Nadam se da će ovaj post na blogu još neke potaknuti na pravi put. Sada idite, ojačajte filozofiju Lean proizvodnje i organizujte svoju industriju!
Izvor za neke podatke i inspiraciju
Inspiracija da napišem ovu objavu na blogu bila je odlična knjiga Michela Baudina i Torbjörna Netlanda, „Introduction to Manufacturing: An Industrial Engineering and Management Perspective“, gdje govore o Kaizenu na stranicama 33 i 34. Cijelu knjigu preporučujemo za čitanje 🙂
Translated with permission from “ The Difference between the Toyota Production System and Lean Manufacturing” by Christoph Roser on AllAboutLean.com.